openBIM for the entire building lifecycle
In the building industry, everyone is talking about Building Information Modeling (BIM). Although digitalization in this sector is still in its infancy, the success of BIM projects realized to date has left many wanting more. However, the potential of BIM is still largely untapped. But one thing is clear. The goal must be the vendor-neutral implementation of BIM over the entire lifecycle of a building.
As early as 2014 Patrick MacLeamy, founder of the not-for-profit organization buildingSMART International (bSi), was emphasizing in his presentations the importance of BIM over the entire lifecycle of a building. Although the slogan “BIM BAM BOOM” (Building Information Model, Building Assembly Model, Building Operation and Optimization Model) caused some amusement, it nonetheless underscored the importance of open, vendor-neutral Building Information Modeling (openBIM) over the entire lifecycle of a building because the lion’s share of building costs arises during operation, not in the design or construction phase. In addition, design errors and clashes early on inevitably result in higher costs during operation later on.
Focusing on the early design phase is not enough
Today’s BIM projects clearly focus on architecture and design, that is, the early phase of a building’s life. For this reason, the “protagonists” of this phase shaped the standards, which revolved around the building’s foundation, core and façade, as well as some interior work.
The use of different CAD systems in a project made it necessary to define data exchange formats. Passing around paper drawings gave way to electronic formats. The only vendor-neutral format that took hold was IFC-4 developed by bSi.
In most BIM (pilot) projects underway today, we are only at the beginning of a much-needed major transformation of old processes. Conventional design taking place in tandem with construction impedes satisfactory coordination of disciplines. Because of current tendering practices, the executing contractors as well as their systems and solutions aren’t known until much later. To some degree, the customer is buying a pig in a poke.
In a BIM project, the entire design process takes place in the virtual part of the digital twin. All the required coordination, simulations and testing can be done in the data model. Physical construction doesn’t even start until the virtual building meets all requirements – a well-established approach in other industries.
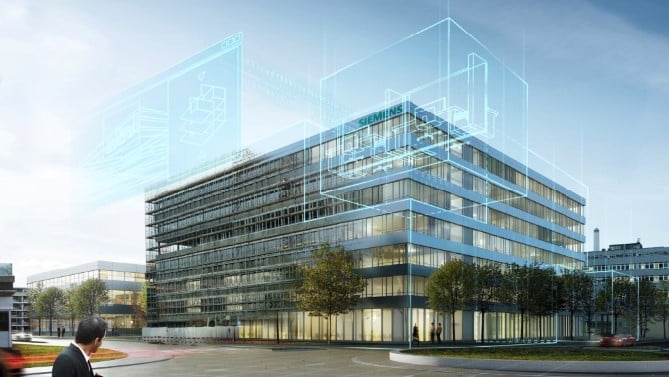
Project databases must become vendor-neutral
Coordinated parallel planning and design, as well as the resulting project data model, form the basis for optimized operation later on because once collected, all the data is available for subsequent use. In contrast to product data, there are still no standardized database structures for project data; only exchange formats have been defined thus far. The frequent use of databases from different CAD vendors naturally creates a certain degree of loyalty to these vendors. The structure of these project databases must be made to be vendor neutral, i.e. standardized for openBIM. Otherwise, applications have to be modified for each project, with mapping being the key word here. Ideally, the project database would be opened with the project and maintained, expanded and used across all phases (idea – design – build – operation – dismantling). The database is as much a part of the building as the cornerstone.
The requirements for these project databases are comparatively high. Considering the useful life of a future, a modular building is 100 to 150 years, it’s clear that the data has to be available for a very long time to cover the building’s entire lifecycle – from design all the way to dismantling. That is a challenge many other industries do not face. It is even more important that we base the structures on vendor-neutral standards. Only when we have the same structures will automated transformation of the data be economically feasible over the long term.
The only organization prepared for this extremely large task is buildingSMART International. This ensures that the standard is defined neutrally and receives international recognition. This is the best preparation for international standardization.
Managing a building with the aid of the digital twin will be more transparent and cost-effective because all the data about the building and its devices and systems are available. For example, installers manually measuring a room for new carpeting will become a thing of the past.
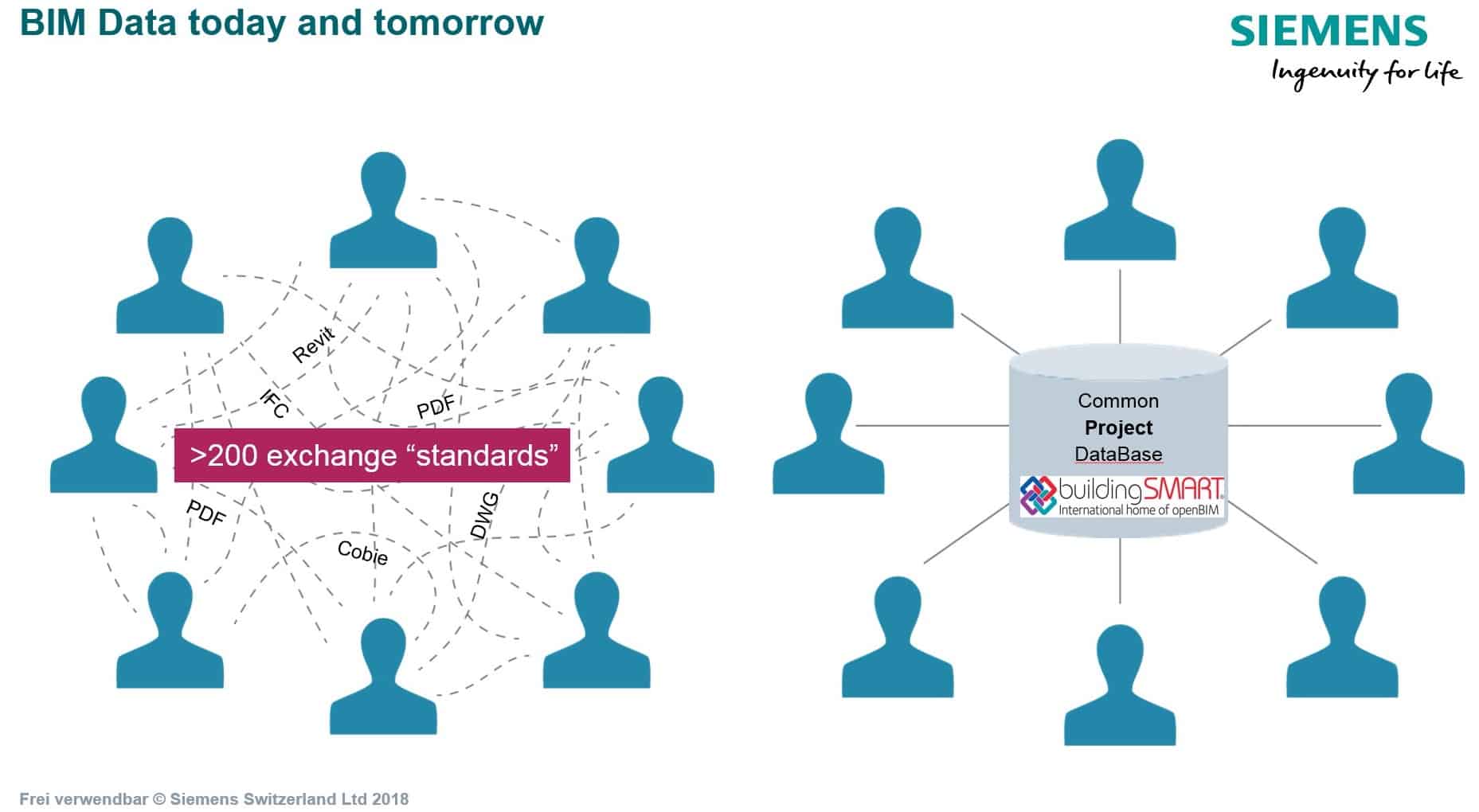
The benefit of preventive maintenance
Of particular interest is the use of data for preventive maintenance because it will enable a direct comparison between product specifications and real-time data. This will make it possible to optimize service calls, for instance. Any needed renovations can be simulated in advance. Likewise, full-on overhauls can be simulated risk-free in the virtual data model to reveal the impact on ongoing operations in advance. Will the renovation violate safety zones? What systems will need to be turned off during the renovations and what will the impact be? Will evacuation routes be guaranteed? BIM can help answer these questions right away.
In addition, knowing precisely which products and systems are installed simplifies stocking spare parts and placing orders. The building becomes transparent for the operators – a transparency that is the basis for fact-based decisions.
The gains realized from increased operational efficiency and optimization far outweigh the initial outlay for BIM. Every penny invested in BIM in the design phase pays off during construction, and once the building is operational, the return on investment is impressive.
Author: Wolfgang Hass, Principal Expert, Siemens Building Technologies